How Does DTF Printing Work? [Updated Guide 2025]
Have you ever wondered how those stunning, detailed designs come to life on t-shirts, hoodies, and other garments? If the answer is yes, you have come to the right place.
DTF (direct-to-film) printing might be the secret weapon behind those eye-catching visuals. This new and innovative printing technology is gaining popularity all over the world. Right now, it’s one of the most versatile printing methods in the custom fabric print industry.
But how exactly does this process work? Let’s get into the meat of direct-to-film (DTF) printing and find what it can do for you.
This blog will dive into the process, breaking down each step to give you a clear understanding of DTF printing.
Table of Contents
How does DTF Printing Work?
DTF printing is a relatively quick process as compared to other type of printing techniques. Here is a breakdown of the process of how DTF works from start to finish.
Step 1: Design Preparation
The process begins with creating or selecting a design. This can be done using graphic design software (RIP Software), choosing colors, textures, and effects as desired.
Step 2: Printing the Film
The design is then printed onto a special DTF film using a DTF printer. This printer uses vibrant, eco-solvent DTF inks that are specially formulated for optimal adhesion to the film.
Step 3: Film Lamination
Once the design is printed, it goes through a lamination process. This involves applying a special clear hot melt adhesive powder layer over the wet ink design of the film. This adhesive will bond the design to the fabric later in the process.
Step 4: Melt the Powder
Once you’ve applied adhesive DTF powder to the film, it’s time to melt it. Place the curing film in the oven for 2-3 minutes. Now, the printed and laminated film is ready for transfer. The fabric to be printed on is prepared by placing it on a heat press, ensuring it is flat and free from wrinkles.
Caution: Ensure you only use an oven for DTF printing because it emits harmful fumes. I suggest fitting an air purifier to your DTF oven to keep fumes away.
Step 5: Transfer Process
The printed film is then carefully placed on top of the fabric, with the adhesive side facing down onto the fabric. The film and fabric are then placed into a heat press machine.
Step 6: Heat Pressing
The heat press machine is set to the required temperature and time settings. It applies heat and pressure to the film and fabric when activated, activating the adhesive layer.
Step 7: Peel Off
After the heat press cycle is complete, the fabric is allowed to cool for a brief moment. Once cooled, the film is carefully peeled off, leaving behind the vibrant design transferred onto the fabric.
Step 8: Final Cure
The fabric with the transferred design may undergo a final curing process, either through the heat press or a conveyor dryer. This ensures the ink fully sets into the fabric, providing durability and washability.
And now you have it: You have completed the DTF design.
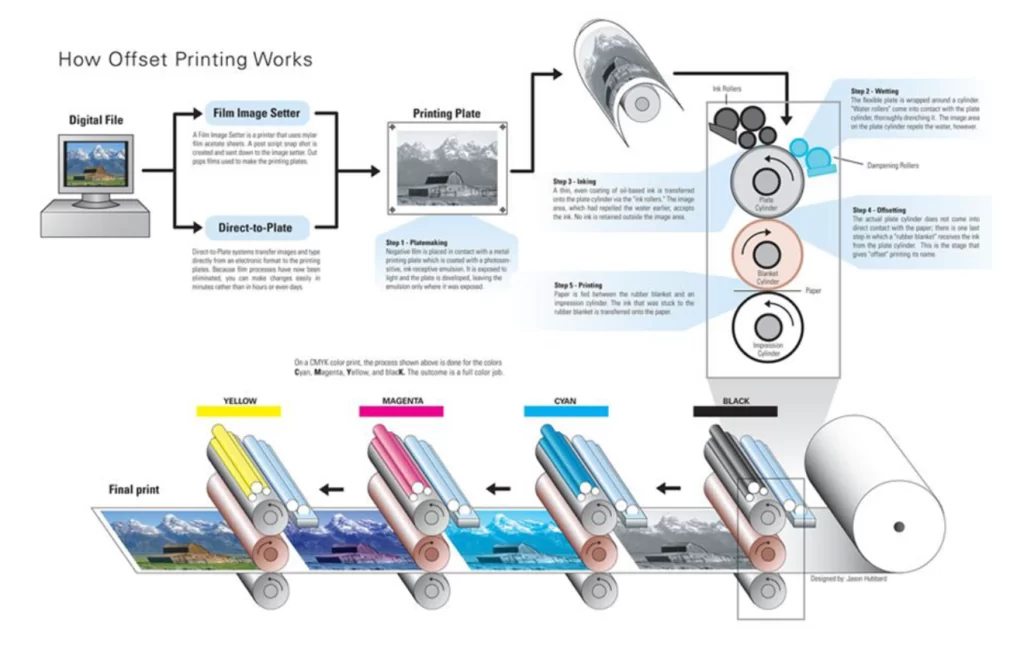
What is DTF Printing?
Direct-to-film (DTF) printing involves transferring designs directly from DTF PET film (a specially coated film that helps in design transfer) onto fabrics. This process cuts down the need for pre-treated garments, unlike DTG printing, where fabrics are pretreated with a special solution.
Most printing methods are limited to cotton and cotton-blended fabric. Still, DTF offers a versatile solution to create detailed, colorful, and durable prints on tougher fabric varieties like fleece, nylon, polyester, blends, and even leather.
What You’ll Need to Do DTF Printing?
Now you better know how DTF printing works! It’s time to focus on the tools and materials you need to invest in to run a direct-to-film printing business. Here is a list of things you need in kit:
- DTF Printer: This is your workhorse. It’s a modified inkjet printer that uses special DTF inks. While regular inkjet printers can be modified, it’s recommended to get a dedicated DTF printer for small businesses to get optimal performance and quality.
- DTF Inks: Unlike regular ink, DTF inks are water-based, elastic inkjet inks designed to work with transfer films. They typically come in CMYKW (Cyan, Magenta, Yellow, Black, and White) configurations. Their elasticity prevents the print from cracking when stretching the garment.
- DTF Film: This is the special PET film where your design gets printed. It has a heat-activated coating that allows the design to be transferred to the fabric.
- Heat Press: A heat press is a must-have tool for the final transfer of the design from the film to the fabric. It is not only used to transfer the film to fabric but also to cure the print permanently. It applies high temperature and pressure for a set time to ensure proper adhesion.
- Hot-melt Adhesive Powder: This fine powder is what binds the design to the fabric. It gets applied to the wet ink on the film and then cured to create a thin, transparent adhesive layer.
- RIP Software: You’ll need design software to create your artwork for printing. If you have a modified DTF printer, you have to download the RIP software to print CMYK and white-colored layers correctly.
- Curing Oven (Optional): While a heat press can be used, some prefer a dedicated curing oven for better temperature control and higher volume printing.
It is also important to know that when you are importing the artwork design into the film certain file formats work with the printer. Some Epson printers can be modified to have DTF printing functions but RIP software must be installed to use the CMYK and white inks.
The file types can be EPS, PS, PDF, BMP, TIF, PNG, and PSD, but cleared background PDF works better. It is recommended to use files with a high resolution of 150-300 DPI for the best results. This will ensure that the prints do not turn out blurry and cheap.
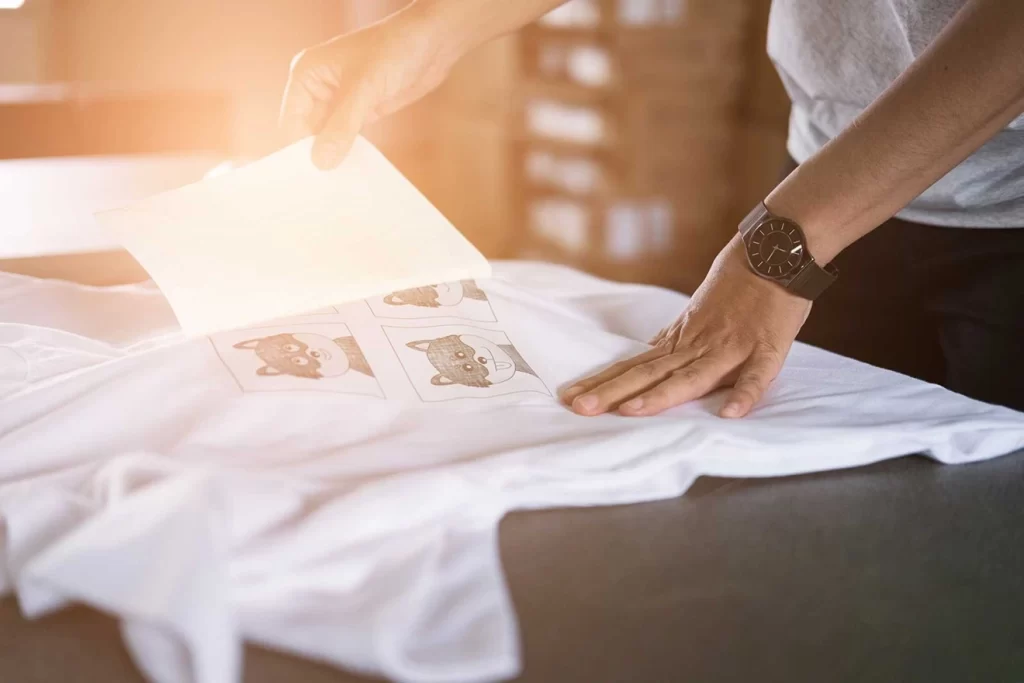
Benefits of DTF Printing
Here are some DTF printing advantages as compared to other printing methods:
- Vibrant Colors: DTF printing offers rich, vibrant colors that stand out on fabrics. Complex designs, photos, and even text come out looking sharp and impressive. Intricate details allow your creativity to flourish without boundaries.
- Versatility: Works on different fabrics, including cotton, polyester, blends, and even leather; opening more business opportunities for garment printing. Unlike some printing methods limited by fabric type, DTF shines with its adaptability. It can flawlessly adhere to a wider range of materials, including dark-colored fabrics, nylon, treated leather, and even non-textile surfaces like wood and metal. This opens doors for creating personalized items that go beyond just t-shirts!
- Durability: The prints are durable, withstanding numerous washes without fading or cracking. DTF prints are known for their resilience. The combination of special inks and a heat-applied adhesive ensures your designs stay vibrant and crack-resistant even after multiple washes. This makes DTF perfect for garments that go through frequent wear and tear.
- Save Time: No pre-treatment is needed like DTG printing which ultimately saves you time. DTF printing has a faster production process as compared to other printing methods. Like DTG printing there is no need for pre-treatment and like screen printing no screen preparation is needed. It saves you both time and energy.
- No Color Limitations: DTF printing allows for full-color designs without additional costs or complexity. There’s no color limitation; you can print unlimited colors and gradients over the substrate.
Downsides of DTF Printing
Like other printing methods, the DTF printing technique also has some downsides that you have to keep in mind while running a printing line:
- Film Handling: DTF film handling is delicate and susceptible to damage if mishandled. Careful handling and storage are required to prevent tears, wrinkles, or dust contamination.
- Film Waste and Environmental Impact: The process generates waste in the form of used films and toxic fumes after transferring the design to fabric. Proper disposal or recycling of these films is necessary, adding to waste management concerns.
- Print Texture and Feel: DTF prints have a different texture compared to other methods like DTG and screen printing. Some users find the texture to be slightly raised or thicker.
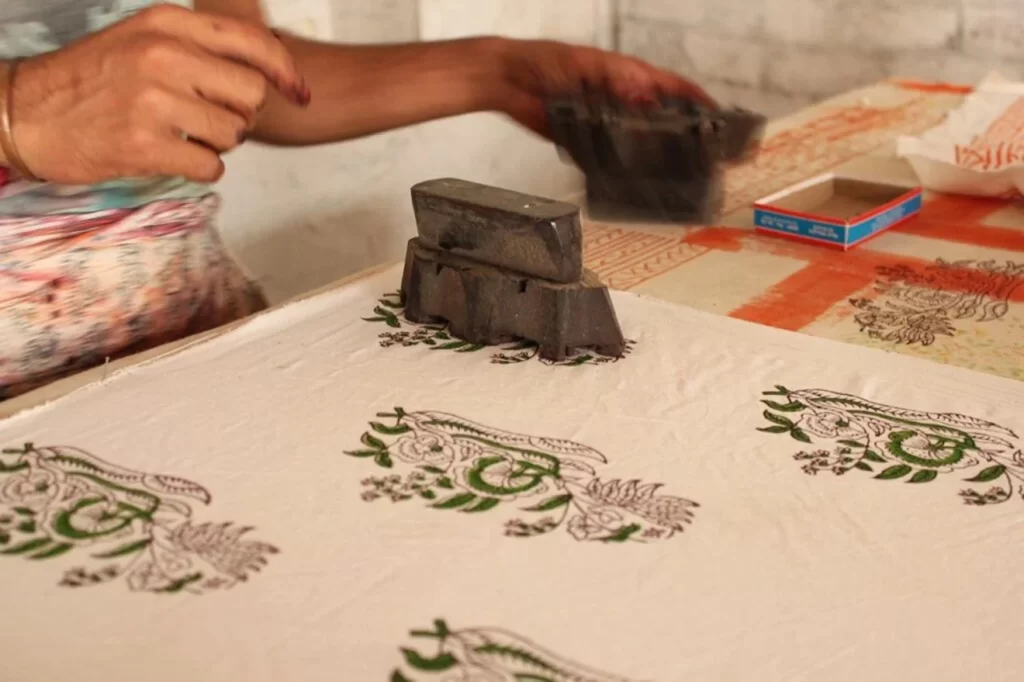
Industries Using DTF Printing
DTF printing has gained immense popularity in a variety of industries due to its versatility and effectiveness. The t-shirt wholesale outlet industry uses DTF printing to customize apparel goods like t-shirts, hoodies, and hats with intricate patterns.
It is very common in the promotional products market, particularly for large t-shirt purchases. It enables industries to produce personalized products like bags, mugs, and phone cases.
DTF printing assists the home decor sector by providing unique and customizable designs on a variety of surfaces such as pillows, curtains, and wallpapers.
Additionally, DTF printing is used in the signage and advertising industries to create eye-catching displays and banners.
Conclusion
Direct-to-film (DTF) printing is a relatively new printing method to customize clothing, bags, and gifts. It’s budget-friendly and an easy-to-run option for a printing line. Due to its convenience over traditional printing methods, you can’t sit back on the bench without cherishing its fruit.
By understanding how DTF printing works, its benefits, and its downsides, you can better explore a new road of creativity and personalization in textile printing.
So, what are you waiting for? Incorporate DTF printing into your print-on-demand business, and expand your product offering with a wide range of high-quality garments.