Tips for DTF Printing Temperature [Quality Prints in 2025]
A trend these days is direct-to-film printing (DTF); it is used to create visually stunning details and patterns onto mostly each garment. However achieving optimal results relies on several factors, and temperature is a key one.
Inaccurate printing temperature can distort images, color bleeding, and poor print quality. When you spend hours and the wrong temperature settings run the design, it can be frustrating. It will not only waste your time but also resources and materials.
But you don’t need to worry about how you will do DTF printing; though it would be your grind’s yield or just a waste of money, theprinterexpert.com is always here to help you.
In this blog, I’ll delve into the importance of DTF printing temperature, the factors affecting it, and its impact on print quality, and guide you toward perfect heat press settings for flawless transfers.
Table of Contents
What is the DTF Printing Temperature?
How DTF printing works is a common question that comes to everyone’s mind. It’s a technique where designs are printed on a film and then heat presses onto the fabric. The printing temperature refers to the temperature at which the ink is actually being cured onto the film.
It guarantees that the print properly adheres to the fabric and the design stays true when transferred to the garment
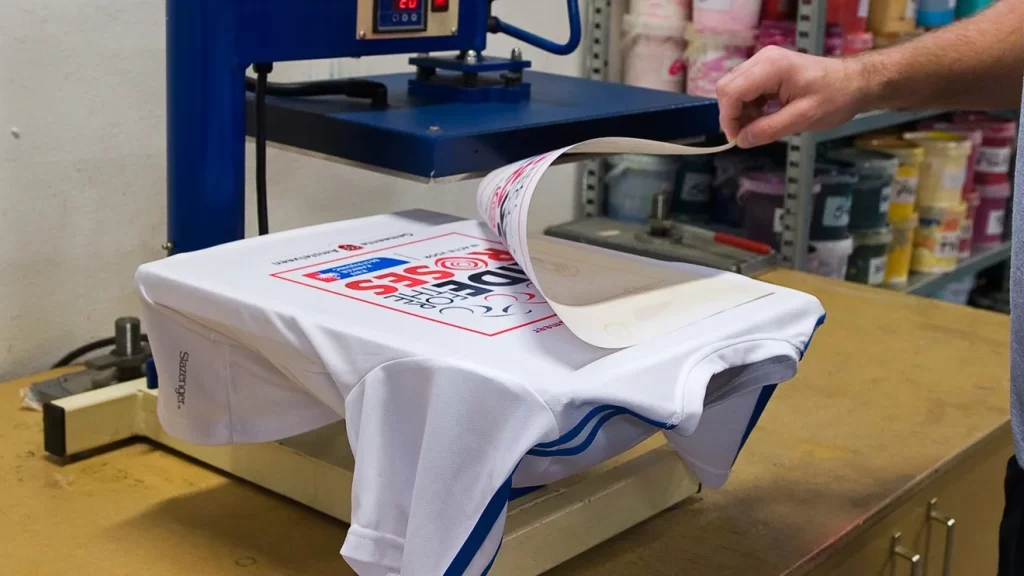
Factors Affecting the DTF Printing Temperature
The ideal temperature for DTF transfers generally falls within a range of 280°F to 325°F (149°C to 163°C). However, this can vary depending on several factors:
Ink Type
DTF ink; maybe it’s CMYK or DTF white ink, each has varying temperature requirements for curing. As you already know water-based inks evaporate at high temperatures, that’s why they usually require lower temperatures.
On the other hand, solvent-based inks need high temperatures for good melting and transfer. It’s always best to consult the specific instructions provided by your ink manufacturer.
DTF Printer
Another factor affecting DTF printing temperature is the type of DTF printer we use. Technology and components determine printer capabilities and temperature ranges.
For example, piezoelectric print heads enable printers to print at lower temperatures than thermal print heads. Printers with a larger print bed also require more heat to keep the temperature steady during the printing process.
Therefore, understanding the printer’s capabilities and controlling the printing temperature is critical. Failure to do so may result in a damaged transfer film, an incomplete transfer, or even damage to the printer.
Fabric Type
The composition of the fabric influences the ideal printing temperature. Some fabrics may require higher temperatures for proper ink adhesion, while others may be more sensitive to heat.
For instance, cotton typically requires slightly higher temperatures than polyester blends. This is just because the cotton fibers need more heat to open up, allowing the adhesive to bond properly.
One of the illest perks of DTF transfers is that these can be applied to any kind of fabric, unlike DTG printing. And their vibrancy and adhesion would be top-notch with different materials.
Below I’ve broken down the three most usual suspect material types and the average temperatures that you should use to press them to print DTF transfers:
Fabric Type | Temperature Range | Time Range |
Cotton | 330°F – 350°F (165°C – 177°C) | 25 – 30 sec |
Polyester | 310°F – 330°F (154°C – 165°C) | 20 – 25 sec |
Cotton-Poly | 320°F – 340°F (160°C – 171°C) | 22 – 37 sec |
These values are a guess, it’s better to consult an expert printmaker. Or follow the manufacturer’s guidelines about the DTF printer, ink, DTF PET film, or material you’re using. Always perform test prints and adjustments to ensure optimal results.
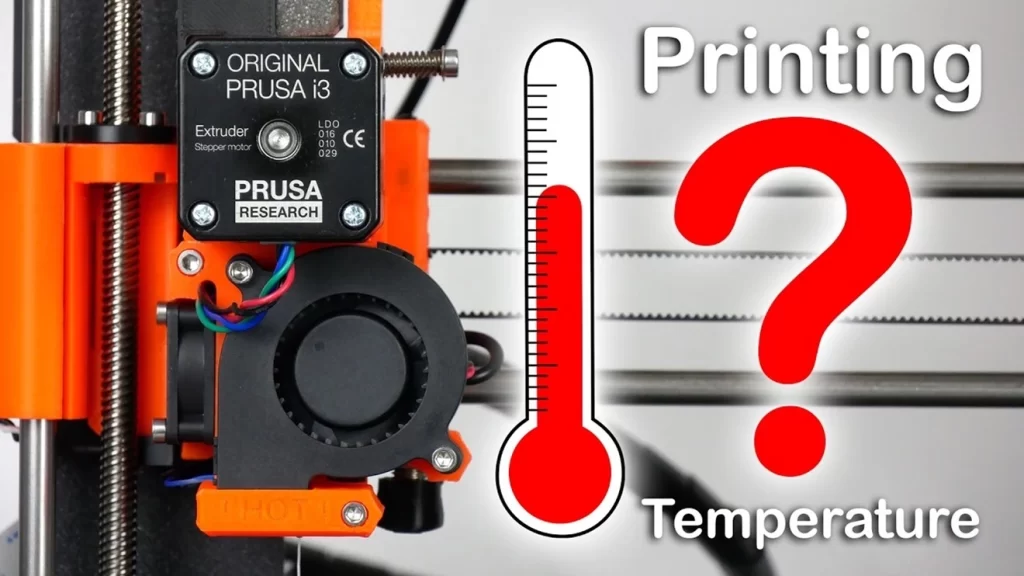
DTF Film Type
Market is full of different types of DTF PET films; hot-peel type or cold-peel type. These films act as a carrier where your design is first printed. Each one requires a different temperature
The ideal DTF printing temperature is characterized by both the kind of DTF film and the thickness of the film. Thicker films may require higher temperatures and longer curing times to ensure complete ink curing and adhesion.
Check the manufacturer’s instructions and recommended settings to apply the film type correctly at the appropriate temperature.
Heat Press Machine
The quality of the heat press machine used in transferring the design is also crucial to getting the desired printing temperature. Not all heat presses are created equal. Ensure your press is calibrated accurately to deliver the temperature you want.
When using a handheld press, pay close attention to the temperature. Start with a lower temperature and then adjust as needed. Again, the temperature will vary based on the press machine, but I recommend setting yours to 320°F.
Press your transfer for around 20 seconds. If the temperature isn’t hot enough, increase it by 15 degrees and try again. Continue to scale until the transfer is properly adhered to the garment.
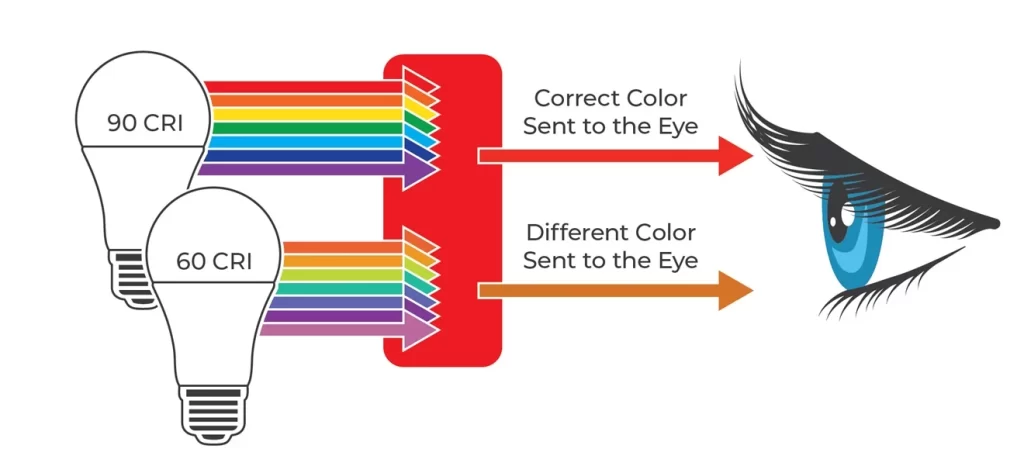
Importance of DTF Printing Temperature
The importance of DTF printing temperature cannot be overstated in textile printing. It determines the quality, durability, and overall success of the printing process. Here are some key reasons why printing temperature is of utmost importance:
- Print Quality: DTF printing produces high-quality prints and saves waste. So, we need to maintain optimal temperature for quality prints. It impacts the final prints in different ways. In case the temperature is too high, the transfer film will destroy itself. The resulting prints would peel or be distorted. In Contrast, if the temperature is too low, the ink may not melt fully to adhere to the substrate.
- Ink Performance: DTF inks are like temperamental artists. If it’s too cold (below 20°C or 68°F), the ink thickens and clogs the print heads of the printer. It causes uneven ink application or printing errors. On the flip side, hot environments (above 30°C or 86°F) can make the ink too runny, leading to smudging or bleeding.
- Ink Curing: The ink applied during DTF printing needs to be cured correctly at a specific temperature range. Improper temperature caused insufficient curing, which is manifested in the lack of a strong bond between the design and fabric. It will not only compromise the ink adhesion but will also affect the washability of the design.
- Transfer Film Durability: The durability of DTF prints is directly linked to the printing temperature. Printing at the correct temperature and following DTF washing instructions enhances the durability of the print, ensuring it withstands multiple laundering without fading and retains brightness over time.
- Adhesion Strength: Proper temperature facilitates strong adhesion between the ink and the film. It ensures smooth design transfers onto the garment without any smudging or fading. Insufficient temperature results in weak bonding, peeling, and cracking of the design after transfer onto fabric. On the other hand, excessive temperature causes overturning, which can also compromise adhesion and print quality.
- Consistent Colors: Maintaining consistent DTF printing temperature across multiple print runs is essential for achieving uniform results and ensuring the reliability of designs. Proper temperature control minimizes variations in print quality and color consistency, enabling printmakers to deliver high-quality products consistently.
- Ink Viscosity: Optimal temperature control is essential for maintaining the desired ink viscosity during DTF printing. At the optimum temperatures, the viscosity of the ink is at its peak for a smooth flow through the printer’s nozzles to ensure that each drop of ink hits exactly where it should. Too low temperatures cause the ink to thicken whereas too high temperatures can make the ink too fluid, causing bleeding on the transfer film.
- Printer Functionality: Just like any other machine, DTF printers have an optimal operating temperature range. Extreme temperatures can stress the printer’s components, leading to malfunctions or shortening its lifespan.

Tips to Ensure Proper DTF Printing Temperature
- That’s a starting point. Always refer to the instructions or suggestions given by the ink manufacturer for the optimum printing temperature range.
- Carry out test prints on sample materials to identify the optimal temperature settings as well as the material that would be best suited for your heat press (improve your current tests you will be able to get better results).
- Make it a habit to routinely tune your heat press machine to maintain accurate temperature regulation.
- Monitor the temperature and humidity of the ambient in the environment that will be used for printing since these levels may affect the curing process.
- Considering the fabric-specific features like its thickness and composition, adjust the printing temperature to the needs of the material.
- Invest in a thermometer or temperature sensor. This handy tool allows you to accurately measure the actual temperature of the heat press plate. It also keeps track of temperature changes that may affect film, ink, or substrate.
- Use a temperature-controlled environment for printing to maintain consistency in prints throughout the operation.
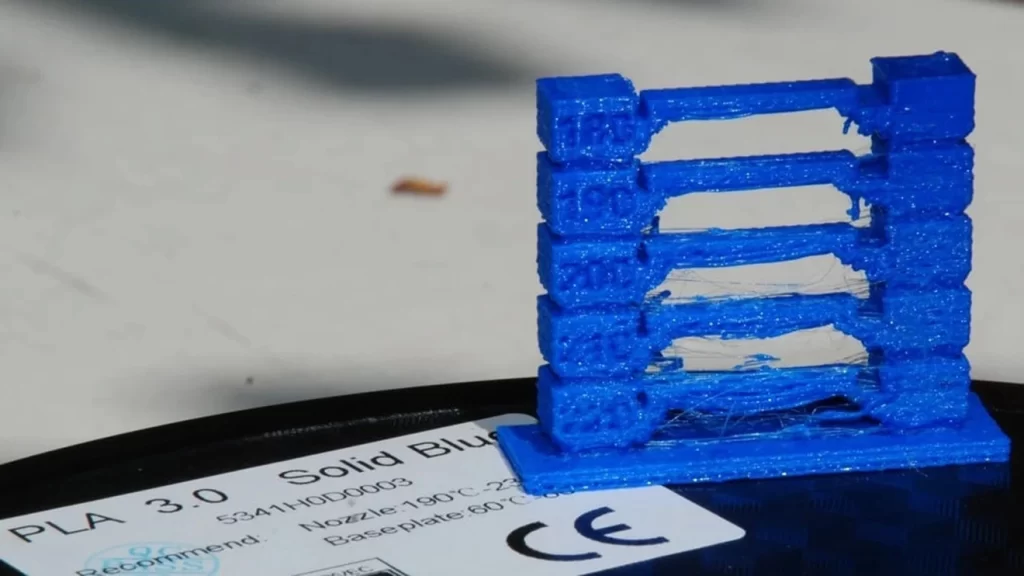
Beyond Temperature: Additional Factors for Quality Prints
While temperature is crucial, remember that it’s just one piece of the DTF printing puzzle. Here are some other factors to consider:
- Pressure: Apply medium to firm pressure during the heat press process to ensure good contact between the film and the garment. The recommended pressure for the DTF heat press is 3-5 kg/cm2 (43-71 psi).
- Pressing time: The pressing time typically ranges between 12-20 seconds, but again, consult your DTF film instructions for specific recommendations.
By understanding DTF printing temperature and considering the other factors involved, you’ll be well on your way to creating professional-looking transfers that last.
Conclusion
DTF printing temperature is a critical factor that significantly impacts the quality and durability of printed designs. The optimum temperature range depends on the ink type, film type, fabric type, and DTF printer.
Knowing what factors should be taken into consideration and getting informed with basic rules would help you get the expected results: bright colors, excellent adhesion, and prints that will be perfectly fine for a long time.
Experimentation, testing, and consulting with manufacturer guidelines are key to mastering the art of printing temperature management.