Common DTF Printing Problems [Solutions in 2025]
Are you grappling with DTF printing problems? Don’t worry; everyone’s got some. It is a relatively new technology, and little has been said about it.
So, to help you with things, I’ve compiled a list of the most common issues encountered in direct-to-film (DTF) printing and their solutions.
Table of Contents
List of Common DTF Printing Problems
Whether you’re an expert printer or a novice, it’s inevitable to come up with different DTF printing problems throughout the process. Addressing these problems is paramount for optimal printer performance and print quality. For this, proper DTF printer maintenance is exercised as a proactive step to prevent potential issues.
After years of research and data gathering, the following are the most common DTF printing problems:
- Ink Compatibility Concerns
- Print Head Clogs
- Image Blurriness
- Ink Smudging
- Printing Speed Problems
- Fabric Compatibility Issues
- Software Glitches
- Film Wrinkling
- Color Inconsistencies
- Ink Bleeding
- White Ink Issue
- Film Peeling Off
Problem #1: Ink Compatibility Concerns
One of the most prevalent DTF printing problems relates to ink compatibility. Just like two humans aren’t always supposed to be compatible with each other, not all fabrics accept all ink types. It occurs if the ink is not able to penetrate the fabric properly.
This happens if you’re not using a pre-treatment solution, or not curing the ink properly. It’s important to ensure that your ink is suitable for direct-to-film printing for vibrant and long-lasting results.
This happens if you’re not using a pre-treatment solution, or not curing the ink properly. It’s important to ensure that your ink is suitable for DTF printing to achieve vibrant and long-lasting results.
Solution: Always verify that you’re using DTF-compatible ink. Substandard ink can lead to color discrepancies and poor print quality. Consult your printer’s manual or the manufacturer’s recommendations for the right ink type.
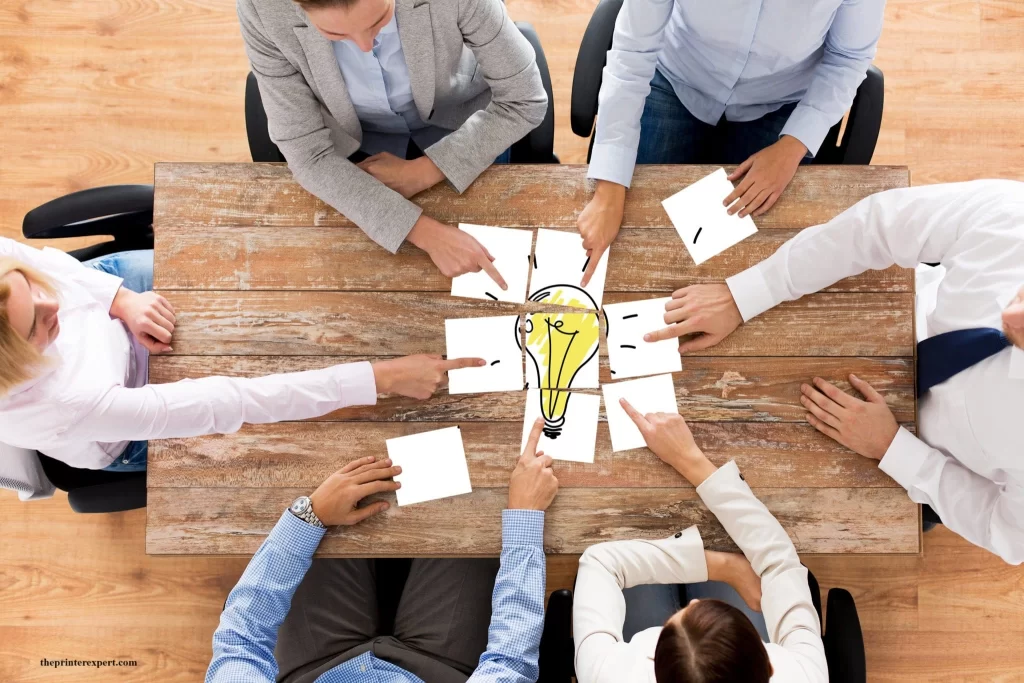
Problem #2: Print Head Clogs
Frequent print head clogs can be a frustrating roadblock in DTF printing. And your roadblocks aren’t good for anyone. These clogs result in uneven ink distribution and distorted images. This occurs when the ink nozzles in the print head become obstructed, resulting in streaky or incomplete prints.
Solution: Regular maintenance is the key. Clean your DTF print head nozzles as per the manufacturer’s instructions. Using a recommended cleaning solution can help prevent clogs and ensure smooth printing.
Problem #3: Image Blurriness
If your DTF prints appear blurry or out of focus, it can be a significant quality issue. It occurs if the film is not adequately stretched and secured onto the printing surface or if the printer is not properly calibrated.
(Nerds like me don’t encounter these issues because we eat our vegetables and read our manuals. I recommend you do that too.)
Solution: Check the resolution of your image files. Ensure they have a high enough DPI (dots per inch) for crisp printing. Double-check your printer settings to ensure they match the image’s resolution.
Problem #4: Ink Smudging
This one reminds me of school. No one likes ink smudges, yet it’s one of the most common problems with DTF printing. It can occur if the ink is not fully cured or if there is too much ink on the fabric. This uneven ink distribution leads to splotchy prints and unsatisfactory results.
Solution: Calibrate your printer regularly to make sure even ink spreads. This adjustment should be performed according to your printer’s manual. Also, confirm the cure of the ink properly and use the correct amount of ink.
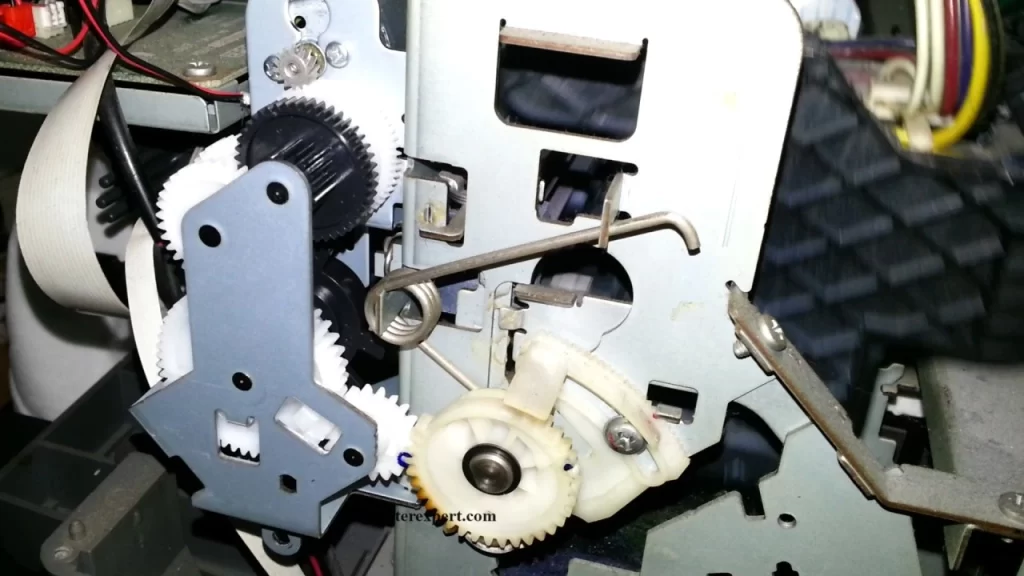
Problem #5: Printing Speed Problems
Don’t let your printer know you’re in a hurry – they smell fear. Printing speed is the main DTF printing problem with printers. When you want to speed up work, the printer slows down. It affects both the quality and efficiency of DTF printing.
Solution: Adjust the printing speed settings on your DTF printer for small businesses. Experiment with different settings to find the optimal balance between speed and print quality for your specific needs.
Problem #6: Fabric Compatibility Issues
What counts in making the best prints is how compatible the ink is with the fabric. Different fabrics require adjustments in the printing process to achieve the desired results.
Solution: Always test print on a sample piece of fabric before printing on your final product. It’ll help you determine the right settings and adjustments needed for each fabric type.
Problem #7: Software Glitches
A printer with glitch-free software is ideal for quality printing. Software-related issues are a common source of frustration in DTF printing.
Solution: Keep your DTF printing software updated to the latest version. Consider seeking assistance from the software provider’s customer support for troubleshooting assistance.
Problem #8: Film Wrinkling
It occurs if the film is not adequately stretched or secured onto the printing surface. So, stretching is just as important for films as it is for us. As a result, wrinkles form on the film, causing alignment issues and distorting the final print.
Solution: To avoid film wrinkling, make sure to stretch and secure the film properly onto the printing surface. Uneven tension and stretching lead to wrinkles on the printing surface.
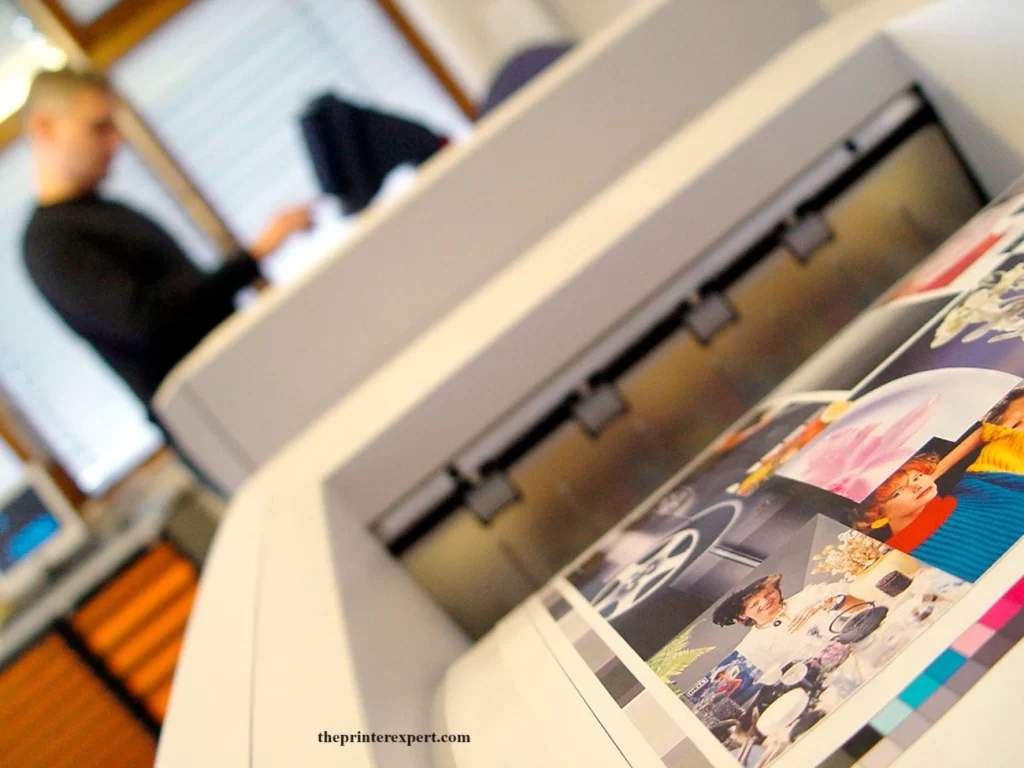
Problem #9: Color Inconsistencies
Inconsistent colors can be frustrating. It occurs if the ink is not properly blended or the printer is not properly calibrated.
Solution: To address this problem, carefully mix the ink and change the printer calibration to ensure that your design files are in the right color mode (CMYK). Besides, maintain consistent environmental conditions to prevent color shifts.
Problem #11: White Ink Issue
When you print on black colored fabric with white ink as the base layer, this is the most seen DTF printing problem. You have noticed white ink does not properly blend and leaves a translucent and uneven layer. It not only turns the final prints in a greyish tone but also affects the vibrancy of the print.
Solution: To cater to this white ink problem, carefully mix the white ink and modify the printer’s calibration setting. Regular maintenance of ink lines is necessary to avoid any kind of ink blockage.
Problem #12: Film Peeling Off
When a final print is done, it starts peeling away from certain parts after one or two washes. It occurs if the film is not properly cured or the fabric is not properly heated.
Solution: To avoid the film peeling off, make sure to cure the film properly and heat the fabric properly. Follow the DTF washing instructions to keep your prints fresh and crisp. The fabric surface should be clean from any type of contaminant. Keep optimal temperature and pressure during heat press.
Problem #13: Film Not Transfer Properly
This happens when the film isn’t compatible with the fabric or the curing process is incomplete. The design doesn’t fully adhere to the fabric.
Solution: Ensure you’re using DTF film specifically designed for your chosen fabric type. Double-check film compatibility with your ink and fabric. Ensure proper curing with the heat press. Clean the heat press plate to remove any residue that might hinder adhesion.
Problem #14: Image Distortion
Image distortion problem is related to film adhesion. It occurs when film stretches or misaligns over the substrate.
Solution: Ensure that the film is properly loaded and the tension is balanced. In addition, look for any abnormalities in the printing process, such as quick speed fluctuations or printhead problems, which can cause image distortion.
Problem #15: Uneven Prints
Despite your efforts to maintain consistent tension and alignment, you notice that some parts of the print have uneven or faded ink coverage. Such inconsistencies in print create an unprofessional impression and might frustrate both you and your consumers.
Solution: Check and adjust film tension to ensure even pressure across the print area. For consistent prints, ensure that the printheads are accurately aligned.
Problem #16: Ghosting
Last but not least, Ghosting is a common DTF printing problem. It is caused by improper fabric locking or insufficient ink drying within layers, resulting in blurry or doubled images.
Solution: Consider using a higher tension fabric gripper for more stability, or change the printer settings to extend the time between printing layers, allowing the ink to fully cure before adding the next layer.
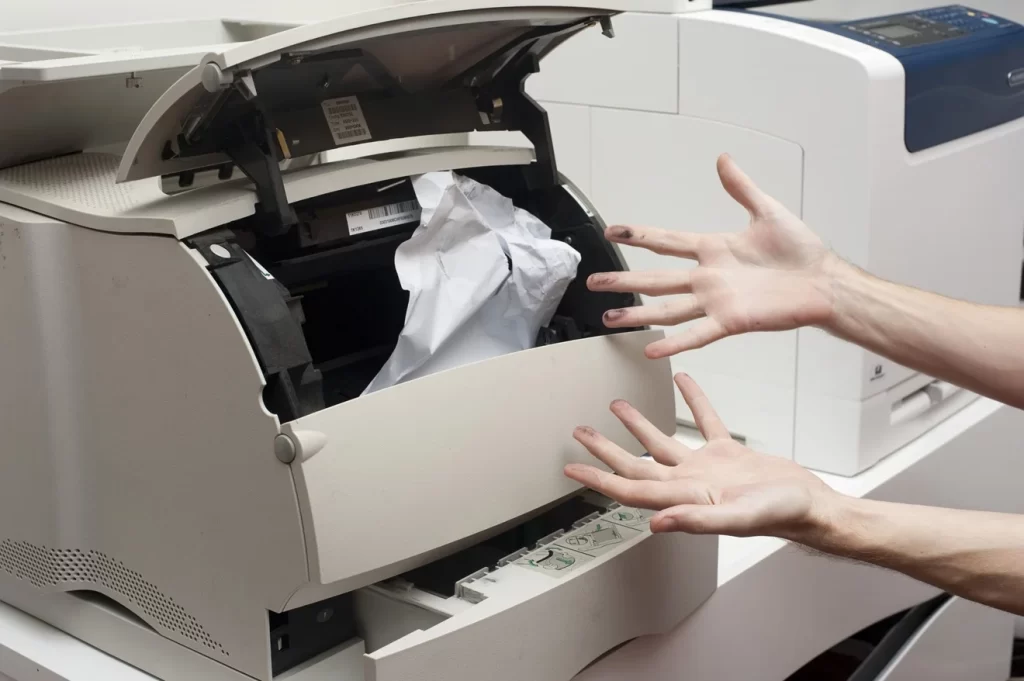
Daily 5-Minute DTF Printer Cleaning Routine
Here is a daily 5-minute DTF printer cleaning routine:
- Wipe down the exterior of the machine with a lint-free cloth and mild detergent or isopropyl alcohol.
- Use manufacturer-recommended swabs or lint-free cloths to clean the inside gently. Do not use cotton swabs.
- Check the gasket on the capping station and clean it if necessary. Ink build-up can cause blockages.
- Without touching the printhead, wipe off excess ink from both sides of the printhead.
- Keep the wiper on the capping assembly clean and check that it is flexible. Don’t use paper towels to wipe the printhead.
By connecting the dots between addressing common issues and choosing the best DTF printer, you not only overcome challenges but also experience efficient DTF printing. This routine will help you to remove any ink or dust that has accumulated on the printer. It’ll also help to prevent clogs and other DTF printing problems.
Conclusion
DTF printing problems can be overcome with the right knowledge and solutions at your disposal. By addressing issues related to ink compatibility, print head clogs, image blurriness, uneven ink spread, printing speed, fabric compatibility, and software glitches, you can improve the quality of your DTF prints for consistent results.
Remember, practice makes perfect in DTF printing, so don’t be discouraged by initial challenges. With time and experience, you’ll become a proficient DTF printer capable of producing stunning, high-quality prints to meet your customers’ expectations.